What are the characteristics of the two common over-current protection methods: shutdown protection and current-limiting protection?
Time:2021-09-07
Views:532
Over-current protection is a standard configuration for power supplies. It can be said that all power supplies have over-current protection. Over-current protection can be divided into shutdown protection and current-limiting protection.
Shut-off protection: When overloaded, the circuit detects that the power supply is over-current, the power chip stops PWM, and it will not return to normal after the over-current fault is removed.
.jpg)
The current-limiting type has the characteristics of current droop, and the switching power supply can automatically resume work after the fault is removed, so it is now widely used. Many chips now have two detection points. The first detection point detects the current overcurrent and turns off the current PWM. When the overcurrent is released, the PWM returns to normal. When the second detection point is triggered, the chip PWM stops and locks. The AC must be powered off to restart.
For current-limiting power supply detection, most of the time we connect a power resistor in series under the MOSFET, and then filter the chip with an overcurrent detection point. R2 in Figure 1 is the current-limiting resistor, and R5 and C4 form an RC filter.
There are several things to pay attention to when choosing the resistance of R2:
1. The resistance of current limiting resistor R2
2. Power selection of current limiting resistor
3. Material of current limiting resistor
The resistance selection of the current-limiting resistor should be based on the maximum peak current Ipk of the primary side and the overcurrent voltage detected by the CS pin. Generally, the maximum voltage on the resistor is 70% of the CS overcurrent protection point voltage, and then according to the set voltage and The resistance value is calculated by the current. After we know the resistance value, the actual power of each cycle can be calculated according to the RMS current of the primary side, and the power required by the resistance is selected according to the actual power consumption. The selected power is 3-4 of the actual power. Times.
After selecting the resistance value and power of the current-limiting resistor, you need to select the material. The current-limiting resistor can be plug-in or patch. When using plug-in resistors, you need to be careful not to use inductive resistors. This is a place that needs special attention.
This resistor is selected to require an accuracy of 1%, and it is a non-inductive resistor. Let‘s analyze what will happen if inductive resistance is used:
First, when the drive is high, suppose that G has a voltage of 12v to ground. When the MOS tube is turned on, because the di/dt is relatively large, the inductance of the inductive resistance may have a positive and negative voltage at this time. The voltage at GS point is less than 12V.
When the drive is low, the voltage of G to ground is 0V, and the MOS transistor is turned off. At this time, the parasitic inductance has a negative and negative voltage. Because the MOS transistor is turned off and no current flows, the current-limiting resistor If the voltage is 0V, then there is a negative voltage on the S pole, and the G pole is 0V, then the voltage between GS and the voltage amplitude on the parasitic inductance are the same. If the parasitic inductance is large, a secondary turn-on phenomenon may occur. Therefore, a non-inductive resistor needs to be selected when selecting a resistor.
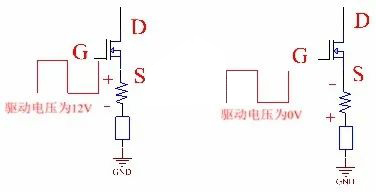
The current-limiting resistor connects an RC to the chip. This RC is used for filtering. Many chips now have a leading-edge blanking function, but the leading-edge blanking time may not be enough, so we still add RC. As you can see in the figure below, the voltage waveform on the current-limiting resistor has a large oscillation. Sometimes the peak of this oscillation exceeds our current-limiting voltage, but this is caused by parasitic parameters and is generally difficult to control. Add RC filter After that, the waveform to point B does not have this oscillation, and is filtered out by RC. The RC is designed according to the cutoff frequency, which is generally 10-30 times the switching frequency. If it is a 60kHz switching frequency, we will choose a 1k resistor and a 100pF capacitor. The approximate cutoff frequency is 1591kHz.
Leading edge blanking is a function of the chip
This function is that after the chip sends out the driving waveform and the MOS tube is turned on, it does not check for overcurrent for a period of time. This time is about 200-300nS, which is different for different chips.
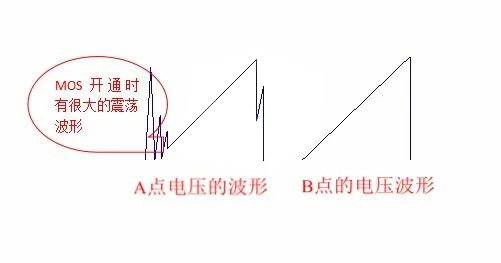
As the power increases, the current of the MOS tube on the primary side will also increase, so the loss on our current-limiting resistor will increase. When it reaches a certain value, the current-limiting resistor needs to select a very small resistance value. A resistance value so small that the parasitic resistance of the traces on the PCB will account for a certain proportion of this resistance value. At this time, the resistance is not easy to choose. At this time, the current-limiting resistor is no longer used, but a transformer is used for current-limiting. The transformer itself is a magnetic device, usually in a ratio of 1:100, which has inductance. We have analyzed the MOS tube earlier. When connecting resistors in series, the resistors cannot be inductive. Now the transformer itself is an inductance, so we need to change the connection method, as shown in the following figure:
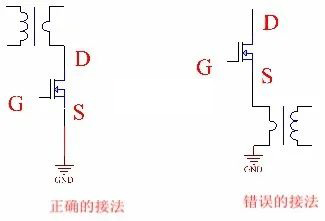
It is necessary to pay attention to the application of the transformer. Its application cannot be connected to the S pole of the MOS tube. Generally, it is connected to the D pole. The reason is the same as the inductive resistance.